With the right instructions, a bitumen welding membrane can be laid comparatively easily on concrete. The material is very cheap, seals well and has a long service life. However, some basic requirements must be taken into account when installing. We offer the appropriate knowledge through tips and instructions.
Bitumen welding membrane: advantages and disadvantages
The decisive advantage of bitumen welding membranes over self-adhesive or cold-adhesive bitumen membranes is the price - the material is significantly cheaper. In addition, the hot gluing or welding ensures a high degree of tightness. Bitumen welding membranes can therefore also be suitable for laying on flat roofs from which rainwater cannot drain away too quickly.
Disadvantage
However, a possible disadvantage is that the bitumen welding membranes have to be attached using a gas burner. They are therefore not suitable for installation on wooden roofs or other combustible materials, as the burner can start a fire. However, this problem can be avoided by using an intermediate length or a cold-bonded layer of bitumen. In addition, there is no danger with a concrete surface anyway.
Difference
Another crucial difference between cold-glued and welded bitumen membranes is the effort required to attach them. Self-adhesive sheets can be rolled out and installed after the roof has been prepared. All you need to do is peel off a film. With the cold-adhesive strips, an adhesive bed is applied and the cut strips are aligned and pressed into place.
Tip:
In the hot process, seams and entire panels have to be processed with the gas burner. This means the effort is significantly higher.
Preparation
Before laying the welding track, some preparatory steps must be taken. These include:
- The roof needs to be cleaned thoroughly. Dirt can reduce the adhesive strength of the membranes. In addition, sharp pebbles or other sharp or pointed objects can drill through the bitumen membrane from the inside and cause the roof to leak.
- Before attaching, the roof must be dry and free of grease. In wet weather, you should therefore refrain from laying the membranes. Alternatively, the concrete surface can be carefully dried with a gas burner.
- The bitumen sheets are cut to size. Ten centimeters are planned as an overhang at the roof edges and around eight centimeters as an overlap between the sheets. Sharp and strong scissors or a cutter knife with a hooked blade are suitable as cutting tools.
- So that the rolls or strips can be laid out, they will be spread out on the roof for a few hours. If the sun is shining very strongly, the bitumen sheets should already be aligned correctly, as the adhesive could already heat up and stick.
Note:
The bitumen rolls should never be stored lying down. Heat can cause the adhesive to liquefy and the sheets stick to one another or stick to themselves. It is therefore better to store them standing up. However, the individual roles should not be too close together.
Instructions for laying - step by step

Once the preparations have been completed, the tracks can be laid. The following order must be observed:
- The tracks are laid from bottom to top. So you start at the bottom edge of the roof. If the roof has no slope, start on the side facing away from the wind.
- The first strip is placed, aligned and weighted - so that it cannot slip during welding. It should protrude ten centimeters on each side of the roof.
- The edges of the web are heated with the gas burner. The heat causes the material to melt and stick to the surface, i.e. the concrete.
- The bitumen welding membrane can be pressed down with a broom and stuck on without wrinkles. Since the broom can no longer be used afterwards, either an old broom or a cheap broom should be used.
- The second bitumen sheet is placed so that the edge overlaps the first sheet by about eight centimeters. Again the edges are heated with the gas burner and pressed and smoothed with the broom.
- Step 5 is repeated until the entire roof is covered.
- Afterwards, the individual strips can be smoothed out again using the gas burner, evenly heated completely and with light pressure. This step is not necessary if a second layer of bitumen is to be applied.
After the first bitumen layer is finished, the protruding bitumen edges are also glued to the roof edges using a gas burner and broom. For a particularly long service life and high level of sealing, it may make sense to attach a second layer of welding membranes. If you want to lay the material in two layers, you don't have to heat the first layer throughout. It is sufficient to simply weld the seams. For the second layer, the material is then heated throughout and smoothed over to create a tightly sealing layer.
Tip:
When it comes to gas burners, it's worth comparing rental and purchase prices. The rental fees are sometimes very high. This is especially true if the device is needed for several days. Therefore, buying a simple gas burner can actually be cheaper than renting it from a hardware store.
Caution: risk of fire
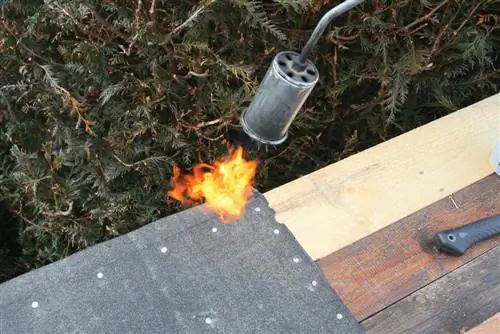
When processing the bitumen welding membrane, there is a risk of fire and injury when using a gas burner. Therefore, the following three safety precautions should be taken into account:
Only on fireproof roofs
The instructions above are aimed solely at laying welding strips on concrete roofs. If it is wood or other combustible materials, either self-adhesive bitumen membranes or bitumen membranes for cold gluing should be used - at least for the first layer. Even then, great caution should be exercised when welding the second layer and the movements should be carried out quickly so that the roof does not become too hot at certain points and burst into flames.
Protective clothing and devices
Protective gloves and appropriate work shoes are just as important when handling the gas burner as it is to have a fire extinguisher within reach. To be on the safe side, the membranes should not be laid and welded alone so that a helper can intervene to extinguish the fire if necessary. Anyone who considers this to be overly cautious should keep in mind that even with professionals, roofs can catch fire due to unfavorable conditions.
Quick work and controls
So that the bitumen membranes do not heat up too much, the gas burner should be moved over the material with quick and even movements. You can then use a stick or rod to check whether the edges of the bitumen membrane are already soft enough to bond to the subsurface and the following membrane. The check usually only needs to be carried out on the first few panels, after which you will develop a feeling for how quickly or slowly the gas burner needs to be moved over the seams and panels to get the right consistency.