The basis for a happy, contented dog life in the open air is a hut protected from wind and weather. Skilled hobby gardeners don't miss the opportunity to build a retreat for their four-legged family member themselves. This is not only fun, but also creates plenty of freedom for individual, creative design. To ensure that functionality and aesthetics go hand in hand, various factors must be taken into account for an optimal design. The following instructions explain how to build an insulated dog house yourself in 7 steps.
The right size
Before purchasing the materials, you should decide on the ideal size of the dog house. The better the dimensions are adapted to the dog's stature, the more comfortable he will feel in his own four walls. It will be too warm for the animal in a hut that is too small. Condensation forms, which threatens rot and mold. If you choose the dimensions too large, the four-legged friend's body temperature will not be sufficient for a warm climate. Even with proper insulation, it gets too cold in the wooden hut in winter. The following rule of thumb may serve as a guide:
- Height of the wooden hut=1, 2 times the shoulder height
- Length of the wooden hut=1, 2 times the length of the dog (from the snout to the tip of the tail)
- Width of the doghouse=1, 2 times the turning width
- The height of the animal at the shoulder defines the height of the entrance.
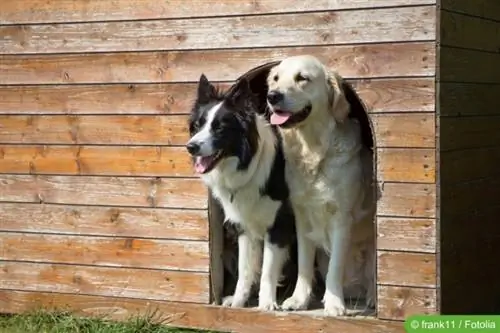
Material and tool list
In a garden close to nature, the main building material recommended is high-quality garden wood that is treated with an ecologically harmless impregnation. In addition, panels made of concrete plan, also known as screen-printed panels, provide additional stability and insulation. A 4-8 mm thick quality made of solid birch or a combination of eucalyptus with a birch cover is ideal, although as a hardwood it is more difficult to work with. The following materials and tools are required when building an insulated dog house with a decorative curved gable roof for a medium-sized dog:
Base plate
- 1 concrete plan in 966 x 656 x 4 mm for the underside
- 1 concrete plan in 900 x 590 x 4 mm for the top
- 2 wooden strips in 900 x 35 x 20 mm for the long side
- 3 wooden strips in 530 x 35 x 20 mm for the cross side
- 1 wooden strip in 320 x 33 x 24 mm for the threshold
Front and back wall
- 2 BFU 100 panels in 695 x 638 x 9 mm for the outside
- 2 Concrete plan in 695 x 590 x 4 mm for the insides
- 4 wooden strips in 590 x 35 x 20 mm for the sides
- 4 curved strips in 350 x 35 x 20 mm
- 2 wooden strips in 325 x 35 x 20 mm for the door sides
- 2 arched strips in 210 x 35 x 20 mm for the door arch
Side walls
- 2 BFU 100 panels in 966 x 55 x 9 mm for the outside
- 2 Concrete plan in 948 x 55 x 4 mm for the inside
- 4 wooden strips in 448 x 35 x 20 mm for the long side
- 6 wooden strips in 481 x 35 x 20 mm as cross strips
Roof
- 1 BFU 100 in 990 x 760 x 4 mm for the top
- 1 concrete plan in 900 x 670 x 4 mm for the underside
- 3 Concrete plan in 635 x 140 x 18 mm as a roof rack
- 2 wooden strips in 900 x 35 x 30 mm as edge strips
Also 4 plastic corner strips and 4 galvanized link hinges as fittings.
Tool list
- Cordless screwdriver
- Eccentric sander
- Hand and jigsaw
- Cartridge press
- Brush
- Sharp drill
- Table saw
- Forcing
Tip:
Since cutting the components is very time-consuming and requires a high level of precision, it is advisable to order this from a hardware store. Cutting it yourself is only worthwhile if you already have the necessary tools in your inventory.
Instructions in 7 steps
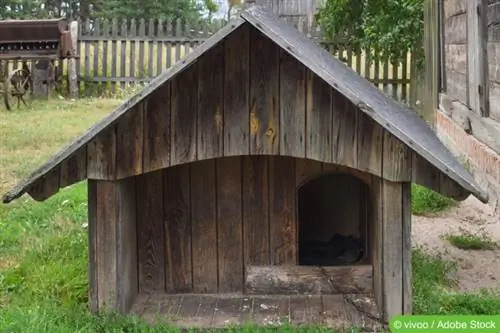
Mounting the base plate
The longitudinal and cross strips of the base plate and the side walls are screwed to the smaller concrete plan plate for the top and the two concrete plan plates for the side walls of the dog house. To prevent the material from tearing, all holes are first pre-drilled. The screw clamps make positioning and fixing the individual parts much easier.
The Isolation
So that your dog feels comfortable in his small home in any weather, insulation is essential. Double-walled sides and bottoms create the ideal conditions. Materials such as Styrofoam, Styrodur, wood wool, sheep's wool or another cold-repellent material are used between the inside and outside. Styrofoam plates are used in these instructions.
To do this, place the side panels and the base plate with the wooden strips upwards to line them with the Styrofoam panels. The sawn outer sides are then fixed with PU glue.
Build an entrance door
To ensure that the decorative door arch and gable shape are uniform, proceed as follows:
- Provide the concrete plan plate for the inside of the front wall with an auxiliary hole
- Construct a simple compass consisting of a wooden strip with 2 holes 500 mm apart
- Screw one hole to the hole in the front wall
- Fit the other hole with a pencil to mark a radius of 500 mm
- Do the same in a radius of 205 mm to mark the door arch
The roof arch and entrance are now sawn out using the jigsaw. This method is then easy to transfer to the back wall.
Sawing out the gable
For correct processing, both gable walls must have exactly the same contour. For this purpose, both parts are braced to create a round roof shape. In addition, both the door side strips and the two door arch strips are positioned and marked on the door opening.
Prepare the strips for the roof structure as follows:
- First align the upper angle of the 4 side strips with the 4 curved strips
- Precisely position and mark all parts relative to each other
- Make sure that there is a closed edge under the round cut
Only cut the length of the strips when they fit together without any gaps below the arch. The side strips are flush with the edges of the front and back. This is where the saw is placed last in this step.
Assembling the gable
Following the accurate preparation in step 4, you can now glue the gable. To do this, align all the strips individually, which is easy to do thanks to the marked markings. Gluing to the inner gable walls is then child's play.
Now we will insulate again with Styrofoam so that the outer gable walls can be glued on. After the drying time, it may be necessary to make corrections with the saw so that the inside and outside sides match.
Build a roof
Now that the gable sides are finished, the gable arch can be transferred to the 3 roof supports in order to saw them into shape. At the same time, it is now possible to determine the exact angles of the roof trim strips and also saw them to size using the table saw. In order to position these end strips precisely, the roof racks must be adjusted. To do this, transfer the dimensions of the end strips and shorten the corners of the roof racks accordingly. Then the roof racks and strips just need to be glued and screwed together.
A helping hand is now welcome to glue the roof framework onto the BFU plate on the top of the roof. In this way you avoid that too long a time passes between applying the glue and clamping it with the clamps.
Final assembly
Now the construction of the dog house will soon be completed, as all that remains is to screw on the underside of the roof. Before you do this, mark the positions of the hinges, which will finally be screwed onto the side walls. These are used to open the roof without tools by pulling out the hinge bolts. The profile strips on the outer corners act as additional protection.
Conclusion
For the experienced do-it-yourselfer, it is a matter of honor to build an individual wooden home for your dog. With these instructions you can complete the project in 7 steps. The result is a decorative dog house with a round gable and correspondingly shaped door arch. So that the four-legged family member feels comfortable in their home no matter the weather, the walls and floor are insulated.