No matter whether it's an aquarium or a yacht, rotten furniture, a laminate floor, a model airplane or whatever - epoxy resin can always be used here. The adhesive and sealing properties of this material are so good that it is not only used for repairs. There are also other positive properties. However, you should know the basics of processing.
Epoxy resins
Epoxy resins are so-called reactive resins. This refers to liquid synthetic resins that can harden relatively easily into a thermoset plastic. The exciting thing about it: The liquid consistency initially allows for versatile and easy use, while the hardened plastic then has an extremely high level of stability. The curing itself takes place at room temperature and does not require much pressure. Given this background, it is not surprising that the material, developed in the 1930s, can now be found almost everywhere.
Typical uses include:
- Construction adhesive in boat and glider construction
- Metal glue
- Mortar based on a plastic
- Cast resin for components in the casting process
- Floor coatings
- Paints, for example as corrosion protection
- Sealants
- Plastination
The range of specific applications ranges from the construction of a glider to the interior renovation of pipes to orthopedic technology. Since the material is completely non-toxic when hardened, it is often used to build aquariums and terrariums as well as model making. Up to now, epoxy resins cannot be recycled and usually have to be disposed of thermally. In addition, they are currently made exclusively from petroleum. However, attempts are already underway to obtain them from renewable raw materials.
Note:
The thermoset plastic that is created after curing is completely non-toxic. The epoxy resin itself, however, can lead to symptoms of poisoning and physical impairments.
Mixture
Epoxy resins are not available to buy ready-made. They must first be mixed before actual use. What you need to know is that the material is made up of two basic components - namely the actual synthetic resin and a hardener. Only when these two components are mixed together in a specific mixing ratio will the desired thermoset plastic be created. In this context one speaks of a stoichiometric resin-hardener ratio. This must be adhered to meticulously, otherwise the desired properties will not be achieved or will only be achieved inadequately.
The ratio depends on the respective product. The manufacturer's specifications for mixing must therefore be implemented precisely. However, these can also be varied under certain circumstances - namely if certain properties are desired. In this way, the hardness or elasticity of the thermoset can be influenced.
Note:
When varying the mixing ratio, you should find out in advance which composition is necessary for which effect.
Processing
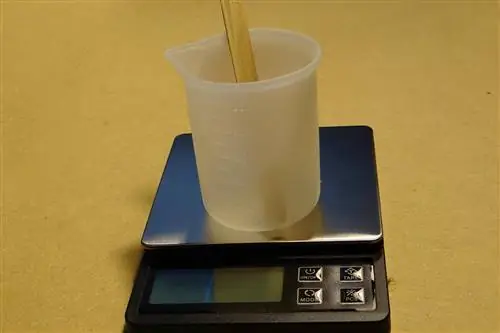
The central basis for processing epoxy resins is mixing the two components in a precisely specified mixing ratio. There is an A component (the resin) and a B component (the hardener). Both are always delivered together. The mixing is done by adding the B component to the A component and then mixing it with it. After thorough mixing, the epoxy resin is ready for use.
Pot time
Pot life is the time in which the mixed epoxy resin can be processed. During this time, the mass remains in a liquid, not hardened state. The length of the pot life depends on the following factors:
- Type of epoxy resin chosen
- Variation of the mixing ratio
- Processing temperature
- Amount of mixed resin
The manufacturer's information on pot life or processing time usually refers to a mass of 100 grams and a processing temperature of 20 degrees Celsius. Larger quantities automatically develop a higher reaction temperature, which in turn reduces the pot life. Basically, the processing time can range from a few minutes to hours.
Tip:
It is better to mix a little less epoxy resin than too much, as too much can quickly lead to the resin no longer being able to be processed.
Application
The use of epoxy resin is called application. This means, for example, applying the compound to a surface or introducing it into a joint. Different tools are used for this, such as a spatula, a spatula, a trowel or even a syringe or an applicator. Which tool you choose depends primarily on the type of application. You should always work as quickly and very carefully as possible. Larger areas must be coated evenly. Excess epoxy resin must be removed immediately, as this can usually no longer be done once it has hardened.
curing
The phase after application up to the finished thermoset is called the curing time. It is usually at least a few hours. It is very difficult to provide precise information about this. They in turn depend on the specific quantity and the processing temperature. Only after final hardening is the workpiece in question fully resilient and usable. Curing can be accelerated - for example by supplying photoinitiators with ultraviolet light. This can sometimes shorten the curing time to just a few seconds.
Protective measures
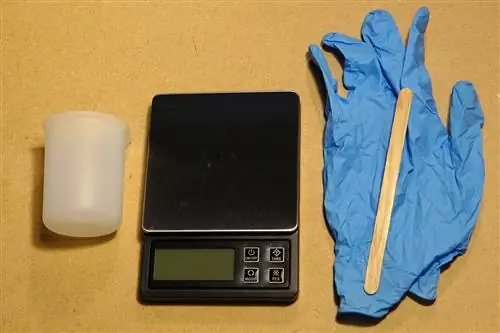
When processing epoxy resins, gloves should always be worn to protect the skin. Both the synthetic resin and the hardener can lead to allergic and very unpleasant skin reactions. Nitrile or butyl gloves as well as PE laminate gloves are suitable for this. Disposable gloves made of latex or vinyl, on the other hand, are extremely unsuitable because these materials can be penetrated by the two raw materials. It is also important to ensure that the rooms are well ventilated. However, wearing a respiratory mask is not necessary.