If you want to call a house your own, you are spoiled for choice. Prefabricated houses, solid houses, kit houses, architect houses and half-timbered houses are just a few examples. However, wooden houses are experiencing a real boom. But not all wooden houses are the same. One type of construction is timber frame construction. Find out everything you should know about it below.
Wood frame construction - meaning
A timber frame building is a construction in which the house's basic structure is made of wood. It represents a kind of skeleton and forms the base. It consists of panel-shaped wall building materials which are attached to load-bearing wooden frames. This creates a robust, stable base. Further stabilization is achieved with diagonally applied boards/battens. The basic production takes place in appropriate manufacturing plants. They are usually delivered as prefabricated elements and are firmly installed on the ground prepared for installation. Further expansion will then take place.
This type is also known as timber frame construction and timber beam construction. At first glance, the new home does not have to be a classic wooden house. It can be combined with countless other building materials without losing the advantages of wooden construction.
History
The timber frame construction is the modern version of the old half-timbered house and is based on the typical lightweight construction method that has been used in North America for centuries. At the beginning of the 19th centuryThe first buildings were built in Germany in the 19th century. Since then, this type of construction has undergone several developments and has now reached a level that offers many advantages for building owners and the environment. The timber frame construction has now become the standard for numerous prefabricated house manufacturers and carpentry shops and is one of the best-selling timber construction systems in Germany.
Wood frame construction advantages
Weather-independent shell construction
The wooden frame construction for a house is delivered prefabricated directly from the factory hall. For builders, this means that no delays due to bad weather or other external influences are to be expected, as often happens, for example, when building a solid structure on site.
Short construction time
Another advantage is that the basic framework can be set up at the future place of residence in just a short time, depending on the size and complexity of the wooden frame construction. The finished shell with roof is usually ready within one to three days. Thermal insulation and windows including window sills can often be ordered as well. This eliminates days or weeks when the builder has to lend a hand or supervise tradesmen to make sure everything is going according to plan. The shortened construction phase allows for faster completion and moving into the new home. Anyone who lived on rent can save additional money on their old rental apartment.
Quick troubleshooting
Each wooden element undergoes quality control before it is sent to the customer. Any quality defects and errors are easier to find and can be corrected more quickly in the factory than on a construction site. If mistakes happen here, fixing them costs time and often the client's money.
Flexibility
As a builder, you have the opportunity to design the floor plan according to your wishes, provided that no specific building regulations prevent you from doing so. Almost any design variant can be chosen according to individual wishes.
More usable space
Wooden frame buildings offer you around ten percent more space inside the house compared to a brick house with identical insulation values. This is due to the fact that there is a smaller wall thickness. With a 100 square meter house outline, this amounts to up to ten square meters of living space, on which you can, for example, set up an additional dressing room or bathroom.
Sustainability and Environment
Wood is an ecological material for environmentally friendly construction. As a rule, the wood for production is sourced from the region or European countries and is not imported from far abroad, where sustainability is not fundamentally an issue when felling. With this design you contribute to climate protection by permanently storing CO2.
Natural thermal insulation
A wooden frame building is provided with insulating materials, but the wood alone already has insulating properties. Wood with a thickness of 6.5 centimeters has insulation values for which 40 centimeters of solid clinker would be required. As a rule, insulation materials made from cellulose and wood fibers are also used, which clearly meet the energy saving guidelines. The difference to other construction methods is particularly clear in the calculation of heating and energy consumption, because heat stays inside and cold stays outside.
He althy Living
Wood is a natural building material that does not require the use of chemical wood preservatives and generally does not contain any other harmful or toxic substances. This not only benefits allergy sufferers and children, who often react sensitively to artificially manufactured building materials. The breathability of wood filters the room air and naturally regulates moisture. In addition, it creates a cozy living atmosphere.
Tip:
When purchasing, always pay attention to the type of pre-treatment, as it may occasionally be the case that harmful substances can be present, especially in the lower price ranges, which are not to be expected with higher quality.
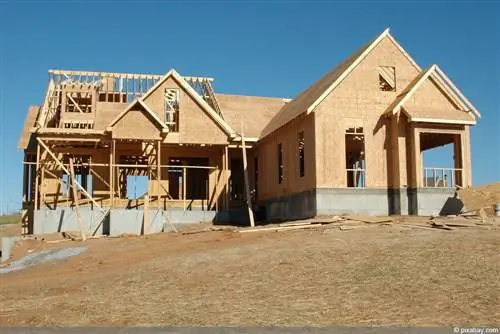
Personal contribution
No other type of construction allows as many possibilities for personal work as timber frame construction. You can have the pure “skeleton” placed on the foundation and, with only a few exceptions, theoretically carry out all the other work yourself. The prerequisite, of course, is that you have the appropriate skills and/or can find expert help from friends/family who can help with the expansion for free or for little money.
The more work you do yourself, the cheaper you can complete your new home. Personal contributions can be, for example:
- Attaching insulation
- Drawing interior walls
- Plastering
- Laying electrics
- Heating installations
- Window and door installation
- Roofing
- Wallpapering and painting
- Installation of sanitary facilities
- Tiles
Wood frame construction disadvantages
There are some disadvantages circulating in society about wooden buildings or a wooden construction, such as the wooden frame construction method. However, most of them are long outdated or are simply prejudices based on ignorance. Nevertheless, a wooden frame construction also has negative aspects.
Fire protection
Concerns are often expressed, especially when it comes to fire protection, which, as a negative assessment, lead builders to refrain from using wooden construction. This is unfounded, because nowadays a timber frame construction is available with the same fire protection rating as can be achieved with a solid house. In addition, wood has predictable fire behavior and, in the event of a fire, can be contained more quickly and combated more effectively than many other artificial building materials. In addition, contrary to some other opinions, wood is a flame-retardant material.
Noise protection
Many people know how old wooden floorboards creak with every step and can be heard throughout the house. With a timber frame building, you don't have to worry about street noise or footsteps disturbing your peace and quiet. The prerequisite is that noise insulation is installed. This is available in different thicknesses and, in the best case scenario, ensures that noise protection is achieved, as is the case with masonry and concrete ceilings.
Tip:
Inquire about appropriate noise protection options from the provider during the planning phase. In many cases, above all, impact sound insulation should/must be provided
Lifespan
The life expectancy of houses with a wooden structure is assumed to be significantly shorter than that of solid houses. Numerous experts have de alt with this in the past and have come to the conclusion that this is the case. In various reports, a difference in lifespan between solid buildings and houses with timber frame construction of 20 to 60 years was found. Accordingly, the durability of wooden beam construction is between 40 and 60 years. The solid construction lasts between 80 and 100 years. As a result, according to the report, it can be claimed that the lifespan of a timber frame building extends over around one generation. Not everyone shares this opinion, but the numbers still serve as a guide.
Resale Value
Due to the simple construction and the relatively short lifespan compared to conventional stone buildings, the resale value is correspondingly low. While the prices for many other types of construction are rising in many places, the value of houses with timber frame construction is generally continually decreasing. This can be counteracted if the timber frame construction ages significantly more slowly and this is determined by an appraiser, including the expected useful life and service life as well as the sales value.
Pests
A once-justified concern about wood was pest infestation. Today, pollutant-free process technology is largely common and standard for many manufacturers/wood suppliers, which makes the wood permanently uninteresting for pests as a food source.
Moisture
Because moisture can penetrate wood, many believe it is particularly susceptible to moisture problems and mold growth. The fact is that moisture usually only collects when there are structural defects, which can be the case with any other construction. Since errors are noticed and corrected at the factory, there is a high probability that the chances of moisture problems with a timber frame construction are lower than with a solid house. Here, the structural defects that cause moisture problems are usually only noticed when they are visible. The condition is always that one of the providers also attaches importance to a flawless, defect-free delivery.
Costs
The costs to be expected for a house with a timber frame construction depend on various factors. The thickness of the wood, square meters, special requests, with or without windows and insulation materials are some examples of the price differences. Of course quality plays a big role. Experts from the construction industry speak of prices for the pure shell starting at around 1,250 euros per square meter of living space including additional costs. You should definitely take a closer look at offers that can go down to 800 euros per square meter of living space. Particularly cheap offers are often explained by a smaller scope of services and/or lower quality.
Caution is particularly advised if larger advance payments or installment payments are to be made before the service is provided. In any case, get different offers, because the price differences can be enormous despite identical purchase and construction plans. We also recommend researching potential timber frame construction providers to find out more about the satisfaction of previous customers.